Interviews
We interviewed Koganei Seiki, a company which continues to produce the world’s highest-class products driven by their professionals, facilities, and shared knowledge, on their relationship with ACCRETECH and the trust between the two companies.
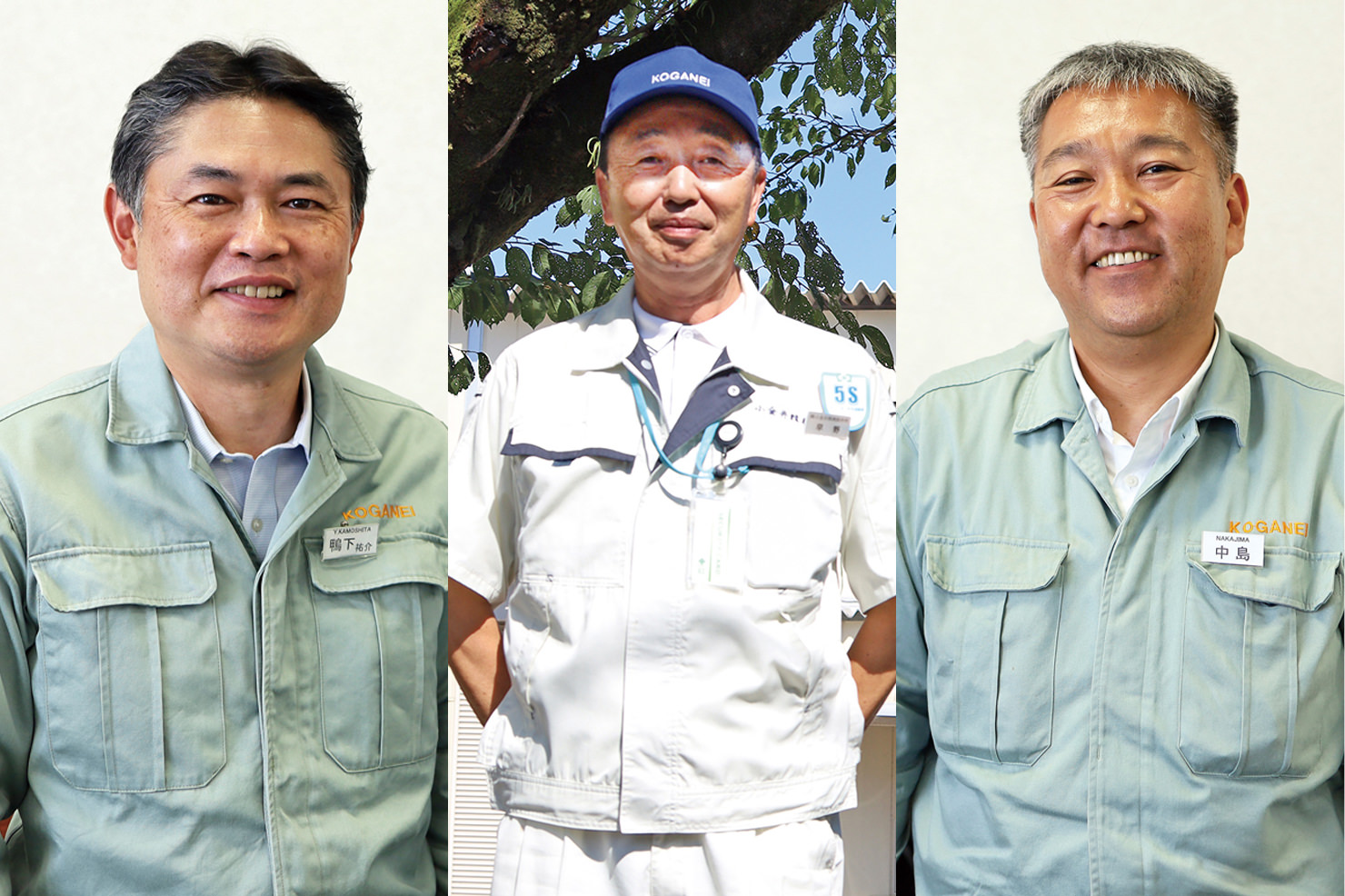
- Koganei Seiki Co., Ltd.
- Koganei Seiki Co., Ltd. President Yusuke Kamoshita
- Koganei Seiki Co., Ltd. Director, Maebashi Factory Head Tsuguo Hayano
- Koganei Seiki Co., Ltd. Director, Sayamadai Factory Head Toshikazu Nakajima
- Koganei Seiki Co., Ltd. was founded in 1943 when it started manufacturing airplane parts. In 1954, the company reorganized into a stock company. With the Sayamadai 1st and 2nd Factories in Saitama Prefecture and the Maebashi and Haruna Factories in Gunma Prefecture, Koganei Seiki has one of the world’s best expertise in high-precision machining of products such as crankshafts, camshafts, cylinder heads, cylinder blocks, and transmissions.
- Head Office and Sayamadai Factories: 4-16-13, Sayamadai, Iruma-city, Saitama 358-0033
Maebashi Factory: 2081, Yamakoda, Shinto-mura, Kitagunma-gun, Gunma 370-3502
http://www.koganeiseiki.co.jp/
Please give us an overview of Koganei Seiki’s business.
Kamoshita: We machine prototype parts such as for automobiles, motorcycles, and next-generation electric vehicles. In addition, we do high-mix low-volume manufacturing of racing vehicle parts such as for Formula 1, Indycar, and MotoGP as well as mass production of aircraft parts. Although I say “mass production,” that amounts to several dozen a month, which is not that different from our automobile prototype production in terms of numbers. Our high-mix low-volume manufacturing delivers 170 to 180 different parts every month, and that is at the core of our business. We have factories in Sayamadai and Maebashi. The Sayamadai Factory processes rotating parts such as crankshafts and camshafts, while the Maebashi Factory machines aluminum castings such as cylinder heads and mills engine components such as cylinder blocks directly from metal blocks.
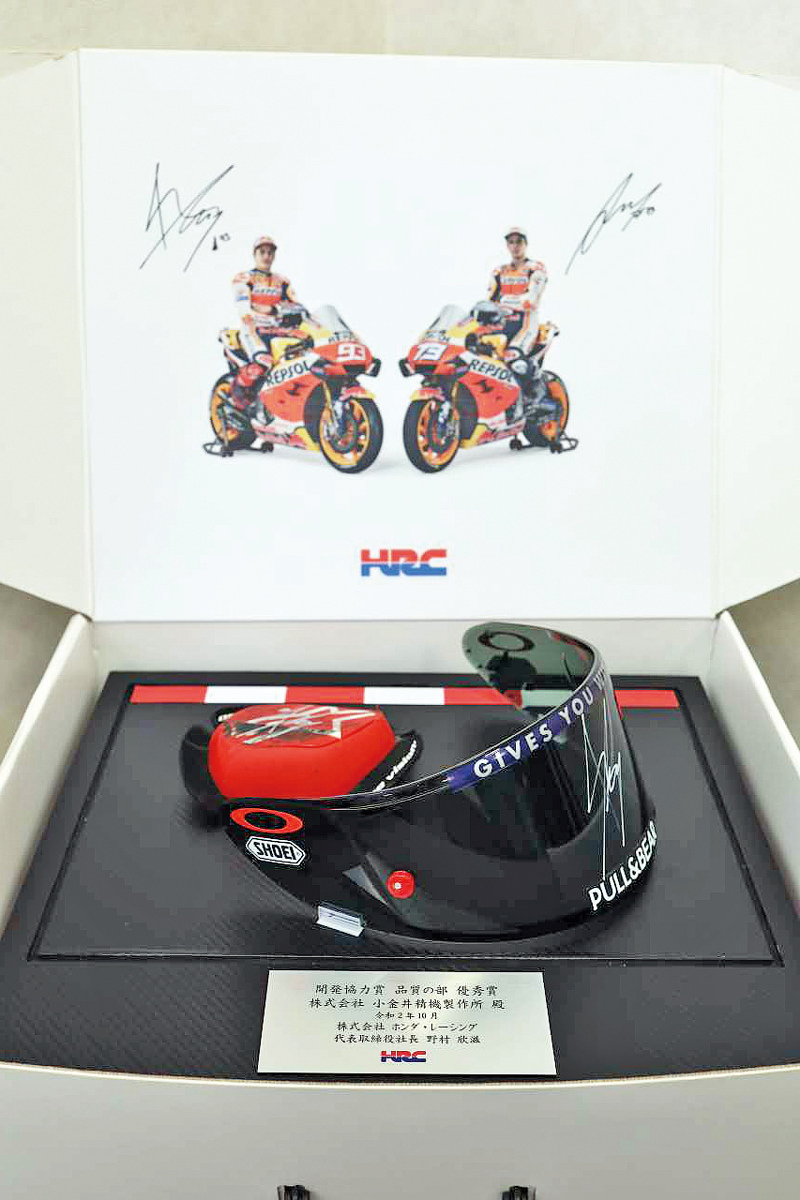
I understand that the company particularly values its employees and facilities.
Kamoshita: All of our staff who are involved in machining know how to use 3D coordinate measuring machines. Of course certified inspectors handle complicated areas, but in general the employees run quality checks on their own work. Our policy is that staff cannot work as machining technicians unless they can use 3D coordinate measuring machines, so that’s the first thing new employees learn how to do. It’s the same whether they are hired as inspectors or as engineers. Being able to evaluate the quality of something you have made enables a self-feedback process for thinking about what to do differently next time. Koganei Seiki is characteristic in that anyone here can do measurement inspections, and ACCRETECH products are characteristic in that anyone can use them. In addition, we have been hiring a lot more women staff for quality inspection in recent years. A team of women currently handle the entire inspection process for our aircraft components. Every year, we also hire university students studying science in Vietnam as fulltime employees due to our company’s strong connection with the country. They are all great assets to the company with their respective abilities. In terms of facilities, we have many machines for precision machining, both made in Japan and overseas. Measuring machines are crucial for inspecting the resulting quality. We mainly manufacture for prototypes, so we value precision above all else, even if it is more time-consuming than mass production. Still, we can’t afford to make customers wait too long, so we use many measuring machines to ensure that there is no downtime waiting on inspection. Currently, we have a combination of twenty-five ACCRETECH and Carl Zeiss 3D coordinate measuring machines. We used to have some measuring machines from other companies, but we are we are trying to make operation consistent across machines by only using ones from ACCRETECH.
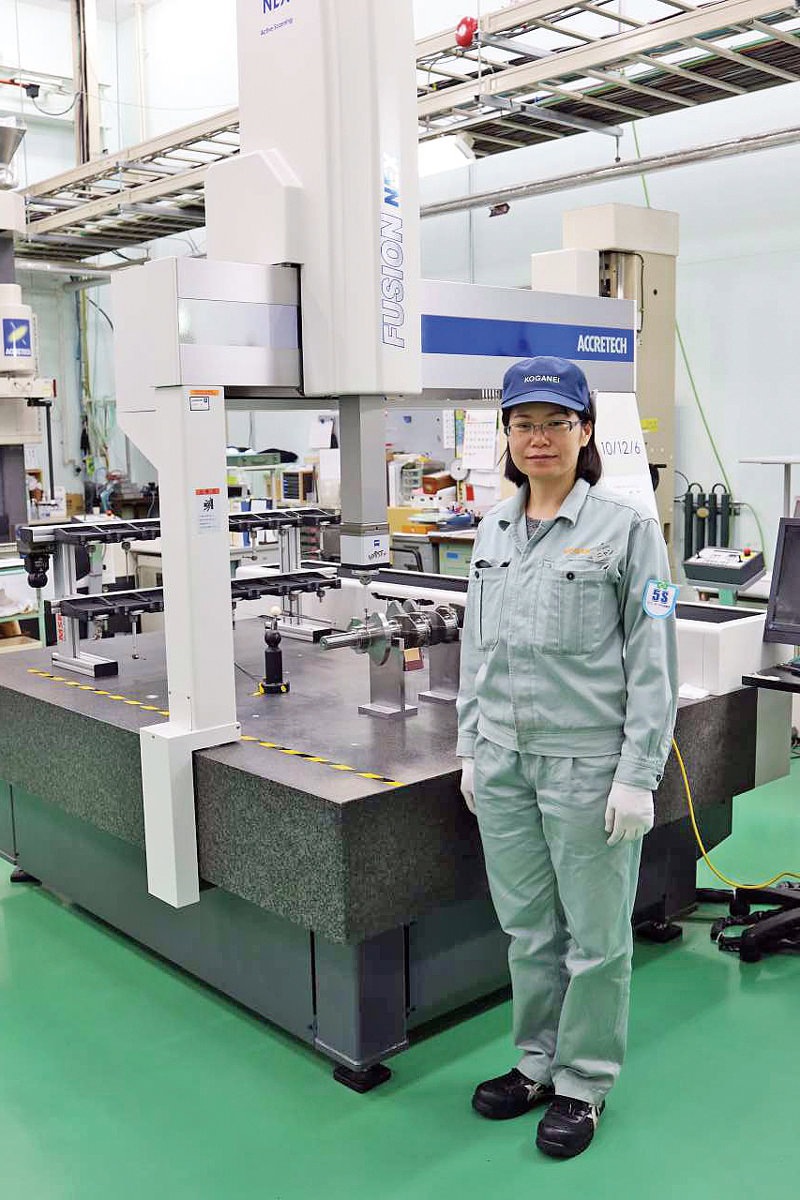
How long have you been doing business with ACCRETECH?
Hayano: Thirty years ago, we started using the roundness measuring instrument RONDCOM 71A, a surface texture measuring instrument, and the 3D coordinate measuring machine WMM850. We’re still using the RONDCOM 71A and WMM850 to this day. Apparently we had another ACCRETECH 3D coordinate measuring machine before that, but that was so long ago that no one left knows the details. That’s how far back our relationship stretches.
Kamoshita: Actually, ACCRETECH once helped us get out of a rough patch a long time ago. We’ve heard that story from the previous president so many times that the entire company feels that we should pass that kindness on and be quick to help if a customer is ever in trouble.
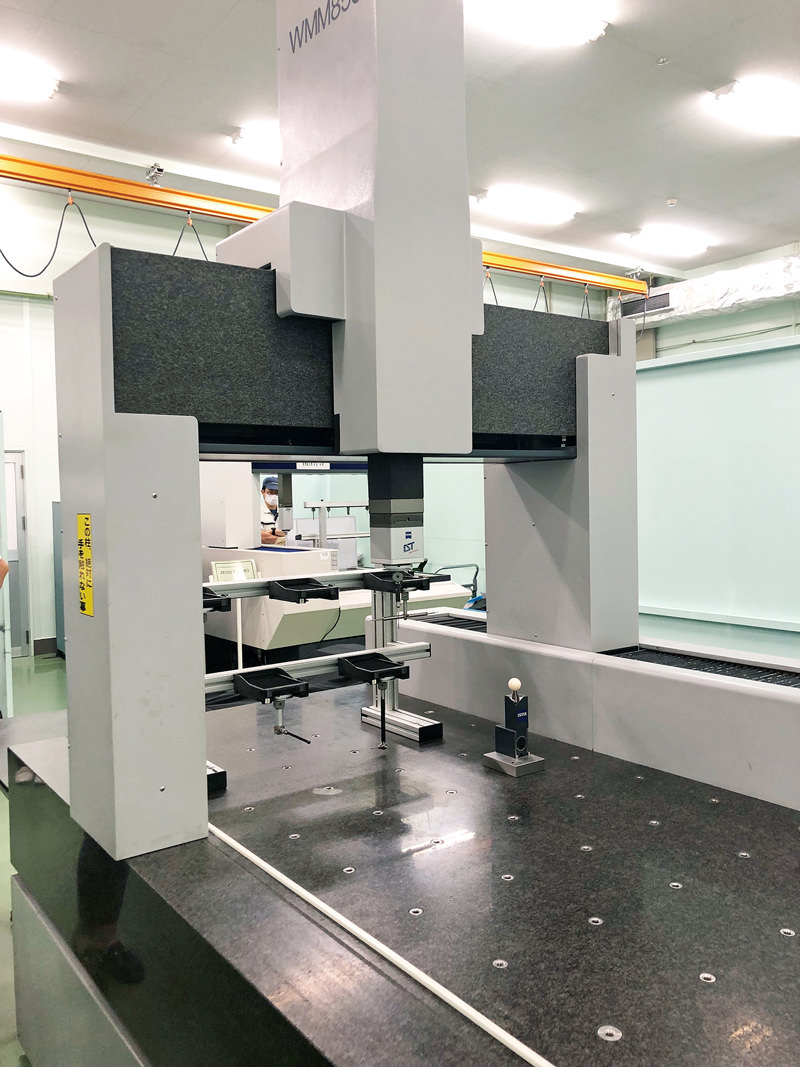
How satisfied are you working with ACCRETECH?
Kamoshita: Our trust runs deep because of our long relationship. Your machines obviously have excellent accuracy, but what we appreciate the most are your maintenance services and your willingness to propose new ideas. Most of the work we do have short deadlines and require speed, so an inspection machine breaking down can be truly detrimental. It is very reassuring that ACCRETECH not only does regular maintenance for us but is also quick to come over and deal with issues even at relatively late hours. Nakajima: The engineers who come from ACCRETECH have always done an excellent job of passing down information on our machines to their successors, and it has been so helpful that even when new people come we do not have to explain anything from scratch. Times are changing rapidly now, and we also appreciate how you immediately offer proposals to match any new areas we want to try going into.
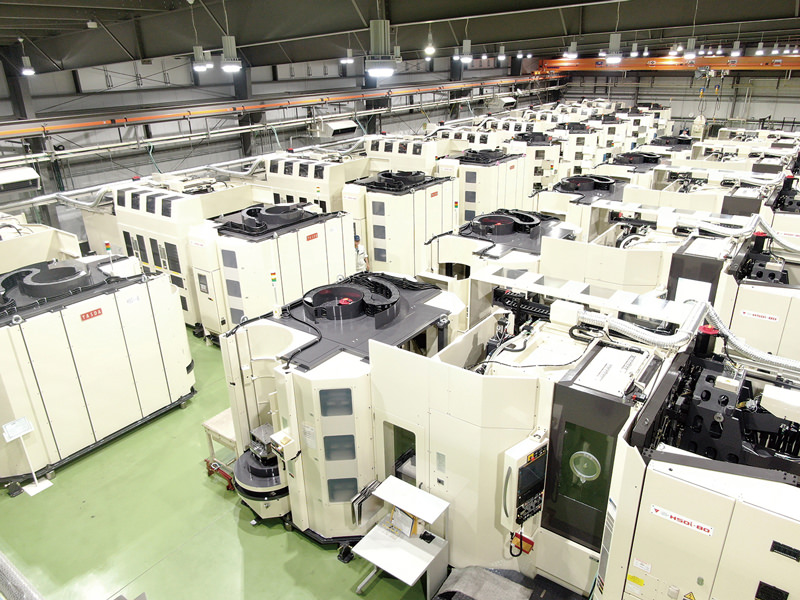
What are your goals for the future?
Kamoshita: We took a serious dive into the aircraft industry five or six years ago. We believe the need for aircrafts will keep increasing as Asian countries develop, so we would like to keep up our efforts there. The automotive industry is also at a turning point towards NEVs. NEVs require precision machining for motor housing and such. In addition to that field, we would like to actively get involved in making components related to wind power generation and other reusable energy sources. Now is a time of rapid change, so we hope to anticipate where society is headed and seize what opportunities we can. We hope ACCRETECH will continue to support us towards these ends the same way it always has.
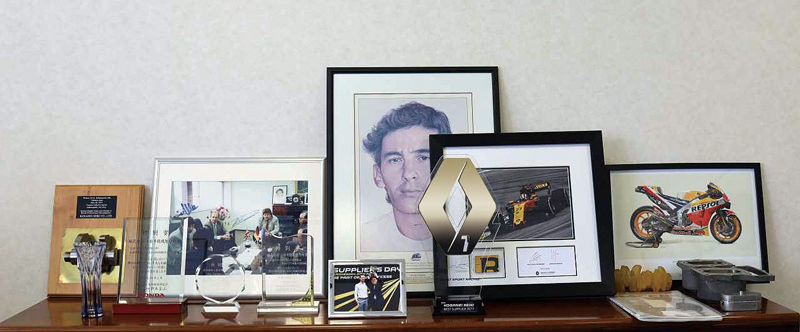
Tokyo Seimitsu’s thoughts after speaking
Koganei Seiki’s high-precision machining on racing vehicle parts for the Honda Motor Co. spread by word of mouth, and now they manage prototypes for many of Europe’s top automotive corporations. And yet, there is a warmth throughout the company that shows that they truly care about their people. They repeated multiple times in the interview that their strength lies in their employees. True to their word, their corporate culture puts emphasis on proper employee education. Employees are able to both process products and run measurement checks to enable high-precision machining.