トップ対談
1944年、愛知県豊田市緑ヶ丘(現本社地)にて操業を開始。主に軸受製品やアルミダイカスト製品等の生産を行い、自動車業界を支えています。さまざまな製品で一貫生産システムを実施しており、鋳造・精密加工・組付・組立・搬送などの多彩な製造技術と高度な品質管理技術を融合させたこの一貫生産の思想は、既存の製品だけでなく、新製品の立ち上げにも素早く対応できるよう活かされています。
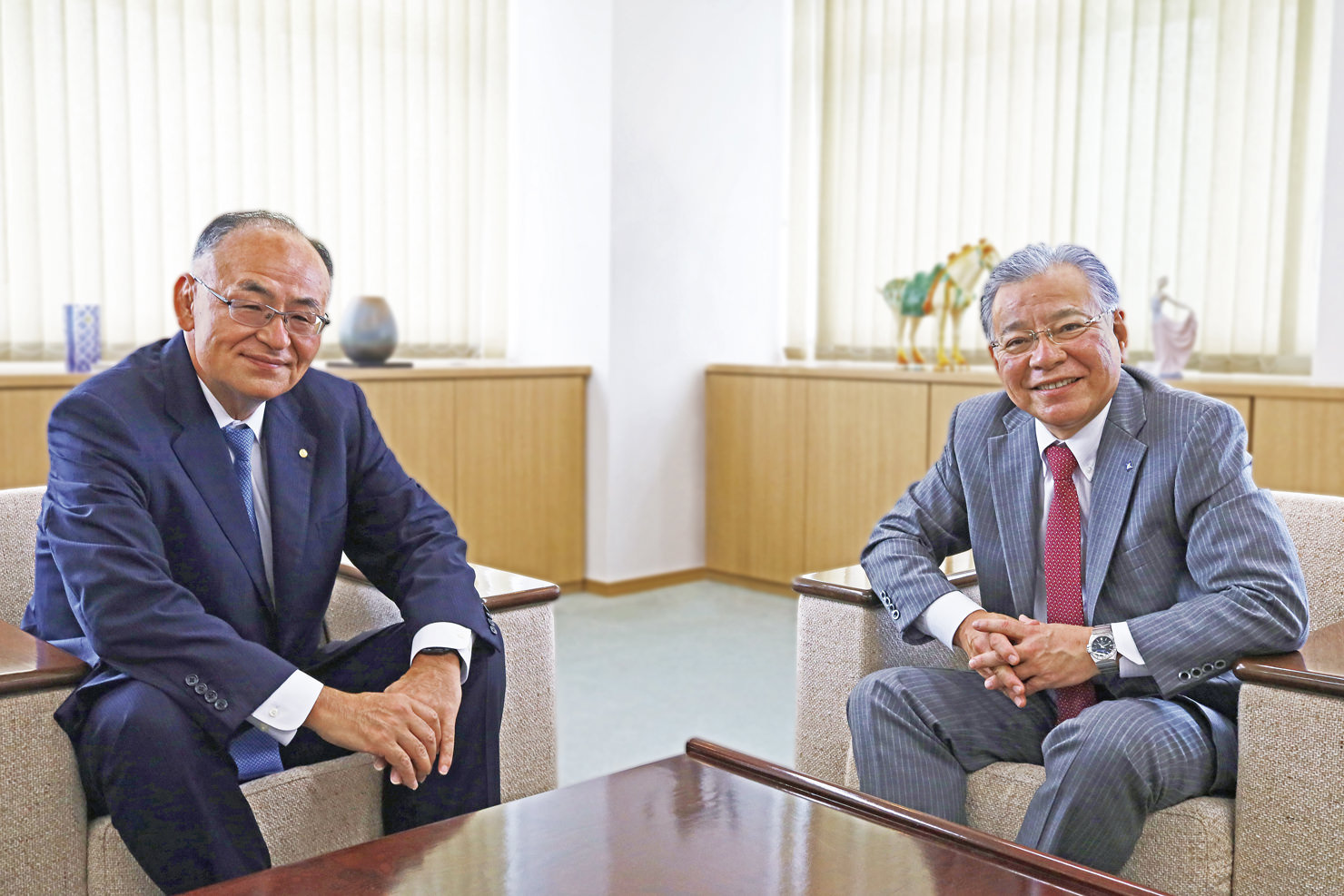
学生時代の過ごし方
吉田 杉原さんはどのような学生時代を過ごされていましたか?
杉原 私は大学に入学と同時に、中学・高校と続けていたラグビーをするために体育会のラグビー部にも入部しました。当時は野球と同じように早・明・慶とも対戦するので、とても厳しい練習が課せられていました。3年時に工学部航空学科に進学しました。工学部は卒業のため卒業論文と卒業設計が必修で、4年時には実験や設計製図に追われる一方でラグビーの練習との両立で大変な毎日でした。ラグビー部のグランドは駒場キャンパスにあり、航空学科は本郷キャンパス、おまけに下宿は東横線の田園調布駅から歩いて15分もかかるので、4年時の私の1日は早朝に起き、まず本郷まで1時間半かけて出かけ、午後2時まで実験と論文製作、それから1時間かけて駒場に移動して午後3時から7時~8時ぐらいまで練習。その後、本郷に戻って深夜まで実験、終電で帰宅ということもたびたびありました。
吉田 なかなかハードな学生時代ですね。その学生時代の経験が今のお仕事に活かされているんでしょうか。
杉原 東京で下宿生活、アルバイトもできないので、親に負担をかけないためにも学部で卒業することに必死でした。ある日、終電で帰って寝過ごして武蔵小杉まで行ってしまったことがあります。下宿に戻るには多摩川を渡らねばなりません。歩ける橋まで迂回するととんでもなく時間がかかります。もう時効ですが、疲れ果てていたので、ショートカットで終電後の線路上を歩いて渡り、下宿にたどり着いたこともありました。随分無茶なことをしたものだと反省しています。しかし、この時代に培われた体力・精神力が、40年以上続く会社生活の中でも活かされてきたと思っています。昨今の働き方改革とは全く逆行していますね。
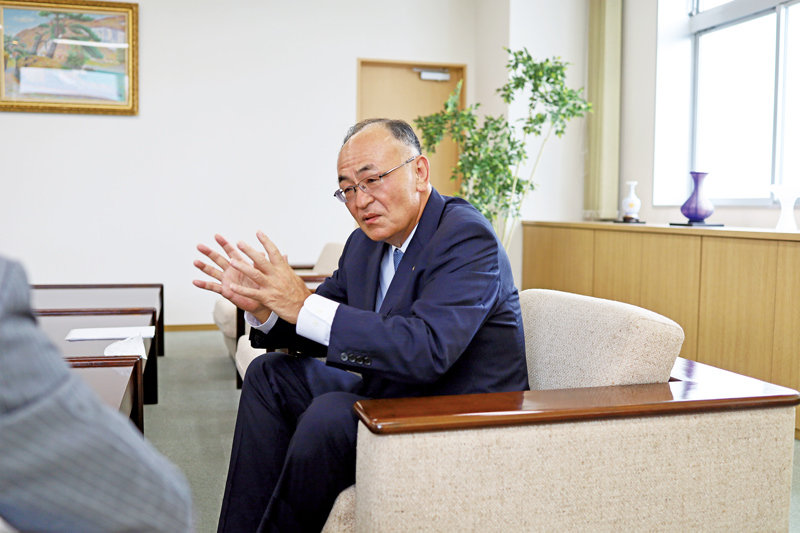
- 大豊工業株式会社
- 代表取締役社長
- 杉原 功一
- 1980年 東京大学工学部航空学科 卒業
- 1980年 トヨタ自動車工業(株)〈現トヨタ自動車(株)〉 入社
- 2009年 同社 常務役員就任
- 2014年 大豊工業(株) 常任顧問就任
- 2014年 同社 代表取締役副社長就任
- 2015年 同社 代表取締役社長就任(現在)
入社時に大変だったこと
吉田 杉原さんはどのような新人時代を過ごされていたのですか?
杉原 私がトヨタ自動車に入社した1980年(昭和55)は、日本の自動車生産が1,000万台を突破し、米国を抜いて世界一になり、トヨタ車の輸出も、初めて100万台を超えた年にあたります。2度の石油危機を経て、日本車の燃費性能や価格への評価が高まり、日本車人気が上昇するなか、一方で、最大の輸出先である米国との間では、通商摩擦が熱を帯び、その後の現地生産化につながるグローバル企業への飛躍が始まった頃でした。
クルマとしては設計技術・生産技術の進化により、駆動・操舵方式が、従来のFR方式(フロントエンジン・リアドライブ)から、駆動・操舵系を前方に集中させたFF 方式(フロントエンジン・フロントドライブ)へ移行し、直進安定性や車両重量軽減に効果を上げました。同時に、小型車の車体長の短縮や車室の拡大のために、エンジン・トランスミッションも大変革され、横置きが主流になりました。日本の優れた燃費性能や価格が実現できたのもこれらの技術開発で先行することができたからだと思っています。変革の時代でしたが、若い技術屋にとっては活気に満ちた、楽しい時代であったと言えます。
そのような時代背景の中、私の配属は、生技開発部という新しい組織で、クルマのFF 化や低燃費化のために必要な部品を量産化する、またはそのための作り方を開発する部署でした。私は小型エンジンの出力向上のためのターボチャージャー、FF化のためのラックアンドピニオンタイプのステアリングなどの内製化に関わる仕事に携わらせてもらいました。
吉田 実際に会社に入ってみて、苦労されたことなどはありますか?
杉原 誰でもあることだと思いますが、学生時代と社会人になってからのギャップはたくさんありました。その中で今でも絶対忘れないようにしていることがあります。自分で設計した部品を機械加工してもらうために、初めて、図面を持って試作工場の職制にお願いに行った時のことです。「こんな図面はお絵かきだ。これでは部品を加工できない。モノづくりには工程があって、その工程を織り込んだ図面でなければならない」と懇切丁寧に教えてくれました。ある工程を経るとその形がどうなるか、次の工程で残る形状はどうなるかを示すのが図面で、単に設計者の必要な形状や公差だけを示しただけではその通り作れないということを教えられました。
トヨタには量産部品の途中工程の状態を順番に示す、工作図という概念があります。これは各工程の品質基準を明確にして各工程で品質を造り込む、いわゆる自工程完結を推進する大事なツールであることを学びました。案外、自工程完結は難しく達成するには設備や品質管理のレベルも上げていかないとできません。工程で造り込みを忘れ、不良品を撥ねる最終工程が正規工程になってしまっている会社も結構あることを知りました。
吉田 配属後、初めて携わったのは何の内製化だったんでしょうか?
杉原 冒頭お話しした、ターボチャージャーを内製化することでした。当社は乗用車用ターボの老舗、米国のギャレット社からの購入しましたが、量が増えるのに応じて内製による自前化を前提にしていました。その内製化チームに配属され、ベアリングハウジングの加工と組付け・評価装置の開発を任されていました。高回転で回る軸を支えるためにエンジンオイルで浮かせたすべり軸受を使うのですが、小径のホーニング仕上げによる、μm(ミクロンメートル)レベルの真円度・円筒度やプラトー面が必要です。その精度を確保するためにエンジンのボア用に使われた古いホーニング機を改造しましたが、ベアリングハウジング用の小径にあう工具はありませんでした。そこで見よう見まねでホーニング工具や、砥石を設計・製作しました。今は20万回転も楽に超えますが、当時は目標の10万回転をクリアするのに何度もやり直しました。組付けでは最終検査装置を作成しましたが、単体評価にガソリンを燃やして排気ガスを使うのはもったいないので、工場エアーを使った評価装置を設計しました。
他にも高耐熱のニッケル合金でタービンを作るためのロストワックス鋳造、インペラを作るためのプラスターモールド法や、クロモリ鋼とニッケル合金の摩擦接合など、初めての技術ばかりで量産化までには大変でしたが、今思えば設計技術から材料・工法まで多くのことを学べた時代でした。
その後は走る・曲る・止る技術がさらに進化して電子制御を取り入れた商品化が進み、内製していたパワーステアリングやショックアブソーバを電子制御化する開発に取り組みました。
89年~ 93年までは、デトロイトに駐在の機会をもらい、燃料電池など宇宙・航空関係の企業や研究所との共同研究をまとめていました。トヨタでは当時から燃料電池に着目し、内製で手の内化しようという計画を持っていました。残念ながら量産車でなかなかFCVが日の目を見ることはありませんでしたが、インフラの整備も整い、25年後の2014年にようやく「MIRAI」が発売されました。
今、自分が経営者になって、当時のことを思い浮かべると、FF化・小型低燃費化に向けてクルマが大きく進化する中で、米国との摩擦を解消するためにグローバル企業としても飛躍をしなければならない。そんな時代に自前主義で将来への布石を打っていた当時の経営者の想いや判断のおかげで今日の発展がある。ただ、現在と違って当時はもう少しおおらかで時間もあったのか、とにかく作って、やってみてから考えようという余裕があったのかもしれません。こだわってやり続けるということも学びましたね。しかし、当時のスピードでは、今の百年に一度の大改革にはついていけないかもしれないですね(笑)
吉田 いやいや。そういった、杉原さんのような方々が切り拓いてくれた過去があるからこそ、今の大改革があるんでしょう。今後、最終的にどういった方向に進んでいくかは分かりませんが、おそらく燃料電池は残っていくんでしょうね。
大豊工業での仕事について
吉田 大豊工業へ入社されたのはいつ頃なんですか?
杉原 2014年にトヨタ自動車から転籍し、2015年に社長に就任しました。もともと大豊工業はエンジン用のすべり軸受(エンジンメタルと呼んでいます)を専門として、76年の歴史があります。私はトヨタ時代に国内外のエンジン工場の担当役員をしていたことや、大豊工業がエンジン部品以外にも駆動・操舵系の機能部品も手掛けていて、私が内製化してきた部品とも縁が深く、もともとなじみのある会社でした。
吉田 杉原さんはこれまで、色々なものを見て経験されてきたと思います。そんななか、大豊工業に入り、最初はどういったところに注目されたんでしょうか。
杉原 生産技術開発部での部品内製化業務に海外駐在も含めて17年携わりました。課長になってからは製造現場に異動して、20年ほど国内、海外の部品工場や車両工場のマネジメントを経験してきました。そのおかげで、どうしても生産プロセスと現場の力に注目してしまいます。
吉田 現場には携わっている人の姿勢も現れてきますし、やっぱり製造業は現場が一番ですよね。
杉原 その通りですね。エンジン用の軸受けは小さな部品ですが、絶対に焼き付いてはならない大変重要な部品です。そのために、粗材は摩擦材料としてのブレンドにノウハウがあり、成型・加工工程は高い精度が必要です。大豊工業はその二つを両立させるため、材料から製品まで一貫して作れる強みを持っています。そして、生産工程には機械加工はもちろん、鋳造・金属アトマイズ・圧延・焼結・熱処理・プレス成型・メッキ・樹脂コーティングなど部品の生産技術としてはほとんどの要素技術がそろっています。それぞれ、奥が深く、現場に行くといまだに新たな発見があり、日々教えられることばかりです。
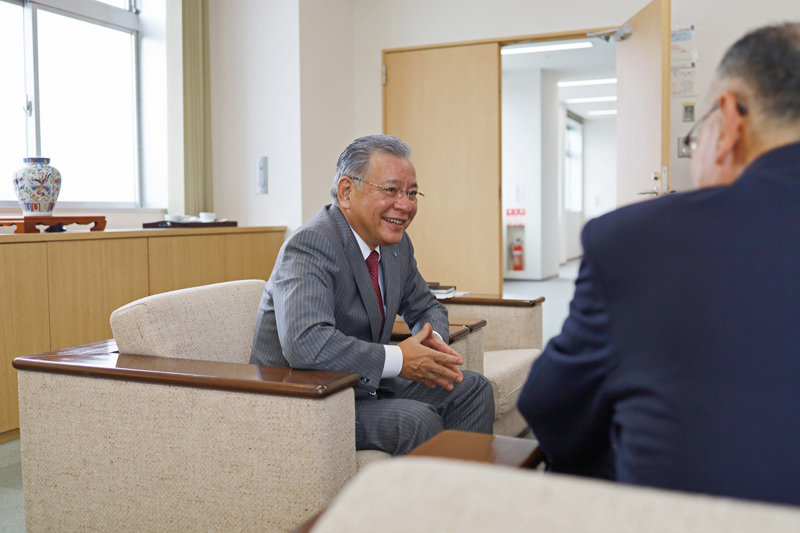
- 株式会社東京精密
- 代表取締役社長CEO
- 吉田 均
- 1983年 明治大学工学部電子通信工学科 卒業
- 1983年 (株)東京精密 入社
- 2010年 日本精密測定機器工業会 会長就任
- 2015年 代表取締役CEO就任(現任)
- 2016年 NDマーケティング大賞受賞
今後の方向感
吉田 会社としてこう変わって行きたい、などの方向感はどのようにお考えですか?
杉原 社長に就任した時の真っ先に感じたことは、組織も個人も横の壁や上下の壁があり、各人の力量にあわせて、よく言えば粛々と仕事を推進していることです。平時にはそれも強みですが、昨今のように変化の速い時代には、会社が一丸となって足並みを揃えて、創造力とスピードを発揮することが必要だと思います。そこで、ビジョンや方針を全社で共有化したり、大豊独自の心構えを作成したり、一体感を醸成する駅伝大会などを開催することで、コミュニケーションを活発にし、壁を取り払いワンチームとなることに傾注してきました。また、上司と部下の関係では特に現場ではOJT(口伝)が主体でしたが、暗黙知が多く人によって教え方が異なります。海外に支援に行くとよくわかるのですが、支援者の力量や教え方がバラバラで現地の作業者が混乱するということもあります。そこで、暗黙知を形式知化することに力を入れ、要素技術に応じたショップ軸毎にテキストを作ってもらい、スキルアップ制度という共通の教え方で人材を育成するプログラムを作りました。そのプログラムで、先輩から後輩への教え方を統一し、教え・教えられる文化をより活性化し大豊の基盤として醸成しています。
吉田 働き方改革と共に、人材育成などの面でも現代は過渡期と言えますよね。弊社でも色んな道を模索中です。
先ほども少し話しに出ましたが、業界の面でも、今自動車業界は百年に一度の大改革の時代ですよね。これから大きく業界が変わって行くなかで、御社としてはどのような方向感をもっておられるのでしょうか。
杉原 弊社の製品はエンジン、駆動の部品が主体ですので、ピュアEV化が進むと経営へのインパクトは大変大きく心配しています。電気・電子部品のようなものがほとんどないので、今後、新しいものを手掛けることを模索しなければなりません。従来部品を「守り」、新規分野を「攻め」とすれば、「守り」では従来部品を磨き深化させ競争力を高めることが重要であり、一方で「攻め」として新たな分野を探索し事業として挑戦していかなければなりません。この「攻め」と「守り」の両立が弊社の生き残りのカギだと信じています。
従来のエンジンに関しては、HVやPHVにはまだ残っており、未開拓の中国市場を含めるとまだまだ需要があるので、そこを狙っていきたいと考えています。競争の要は価格になってきていますが、価格に加えてもう一段競争力をつけるための工法開発や設計技術なども充実させています。価格と精度の両立が必要です。
吉田 精度を上げつつ、コストも下げつつ、ということですね。確かに精度はこれからさらに求められてくると思います。しばらくの間、エンジンは全くのゼロではなく、ハイブリッドの時代になってくると考えています。そして、エンジンだけではなく軸受も含めしばらくは残る。そうなると燃費や音だとかが追及され、それに伴い更に高い精度が要求される、という流れになると予想しています。
杉原 中国では政府主導の電動化も進められていますが、一方でモータリゼーションが進んでより高速で走れて、航続距離も伸びています。高出力・高回転でも焼きつかず、信頼性の高い、日本のエンジン軸受けを求めるOEMからの引き合いは増えています。また、ガソリン車だけでなく、ディーゼル車においても国6(ユーロ6)規制への対応のため、より圧縮率を高くして燃焼効率を上げようとしています。そのため、より高い面圧でも耐えうる軸受け材料が求められています。弊社の材料技術を活かせる分野として、中国の素材拠点も強化しています。
トヨタも大豊工業も古くから東京精密さんの各種精密測定機器に大変お世話になっています。特に私のかかわった機械加工のラインでは、ラインの内外や測定室で内外径・真円度・円筒度・平面度・粗さ・形状精度などあらゆる分野で使わせていただきました。私は生技開発時代、急ぐときには、自分で設計して試作したものを自分で測定していたので、大半の測定装置は使えましたし、当時はアナログ式の時代で、測定前の治具の準備や芯出しもできるんです。今ではそういった芯出しなどは自動で補正できてしまうので自慢にもなりませんが。そのころの量産の加工ラインは、単体の専用機を流れ化でつないで作る専用ラインが主流でした。大量生産には向いているのですが、種類が増えてきたり、設計変更があると段取り替えに大変時間がかかりました。今は汎用機の性能が上がり、複合加工もできるようになり、工程集約されたセル方式が主流になってきました。必然的にライン内に置かれたいくつもの専用測定
器から、汎用の3次元測定機でまとめて測定する時代に変わってきました。測定機器も私の時代はアナログからデジタルへの時代ですが、ハード・ソフトでさらに深化していますね。
吉田 当社でも従来の接触式から非接触へと時代が変わってきており、これからも非接触のニーズはさらに高まってくると予想されます。よりコスト削減をと考えると、スピードタクトを上げることが大事なので、インラインで加工しながら測定してフィードバックまでできるといいなと考えています。今後、我々もチャレンジしていかないと他に広がりがなく終わってしまう。大豊工業さんのようなお客様と一緒に、新しいことに挑戦していきたいです。
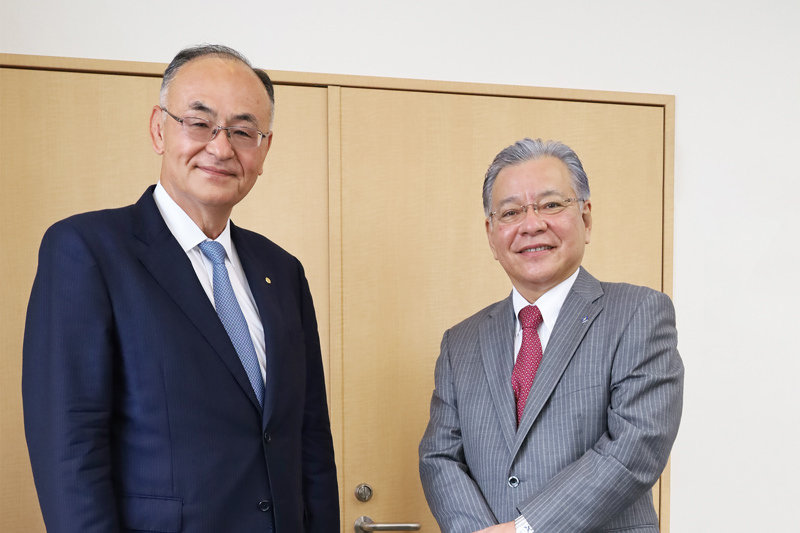
大豊工業株式会社
1944年、愛知県豊田市緑ヶ丘(現本社地)にて操業を開始。主に軸受製品やアルミダイカスト製品等の生産を行い、自動車業界を支えている。さまざまな製品で一貫生産システムを実施しており、鋳造・精密加工・組付・組立・搬送などの多彩な製造技術と高度な品質管理技術を融合させたこの一貫生産の思想は、既存の製品だけでなく、新製品の立ち上げにも素早く対応できるよう活かされている。